Contemporary traditions – the creation of modern and appealing doorknobs and knockers – is the fruit of an ongoing collaboration between Funderija Artistika Chetcuti x Maltadoors, who’s customised designs have elevated door accessories to functional fine-art sculptures.
The door knocker has a long, complicated and somewhat dark history, going as far back as Ancient Greek times.
Although it is common on the doors of traditional Maltese builds, the feature is by no means exclusive to the islands – just like the cement tiles, for instance, says Maltadoors’ Lisa Gwen, who has been documenting local houses and façades for years and is one half of the Contemporary Traditions project.
The ħabbata, as it is known in Maltese, also comes in a knob and handle version on some doors.
It is generally the door style and timber paneling that dictate what design option to use, as well as the size of the desired accessory, she explains, having now shifted her focus to their contemporary design.
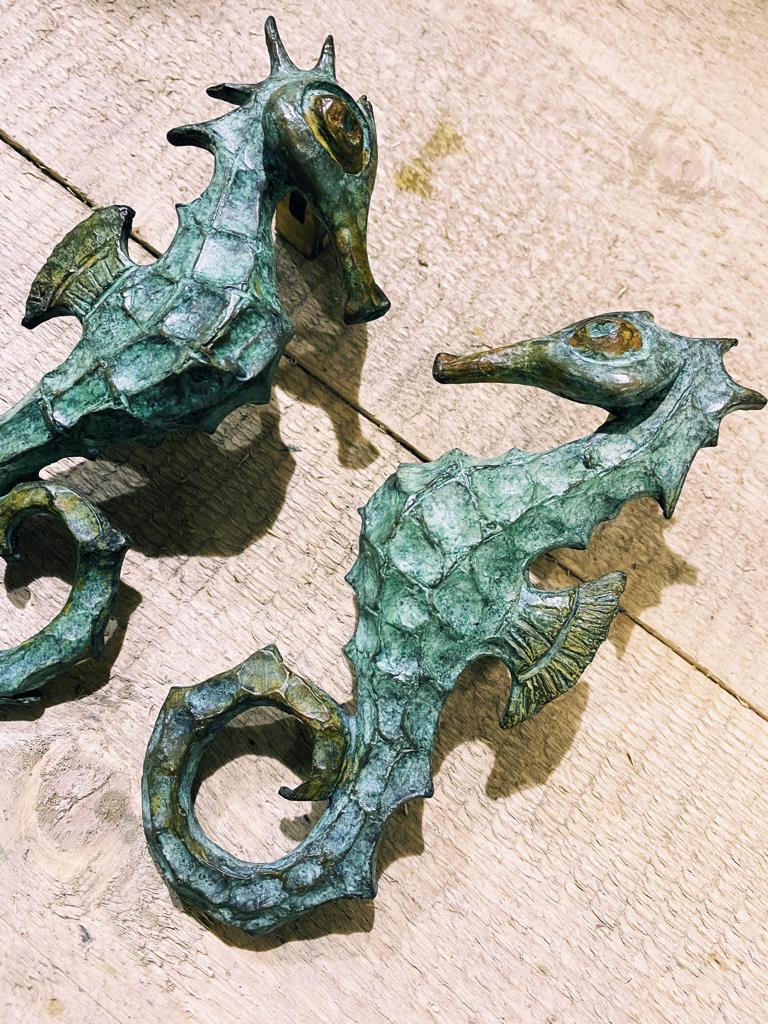
Knobs, knockers and handles generally come in a wide variety of shapes, sizes and materials – the most common being brass, but occasionally, also ceramic, glass and bronze.
It is rare, however, to come across an uncommon or customised design for a doorknob or knocker – and these are generally found on larger palazzos, band clubs, or high-end businesses.
The dolphin, the elephant head, the hand, and motifs incorporating the eight-pointed cross are just a few of the prevalent and most recognised designs adorning Maltese doors.
This is the context in which the collaboration between Maltadoors and Funderija Artistika Chetcuti was born.
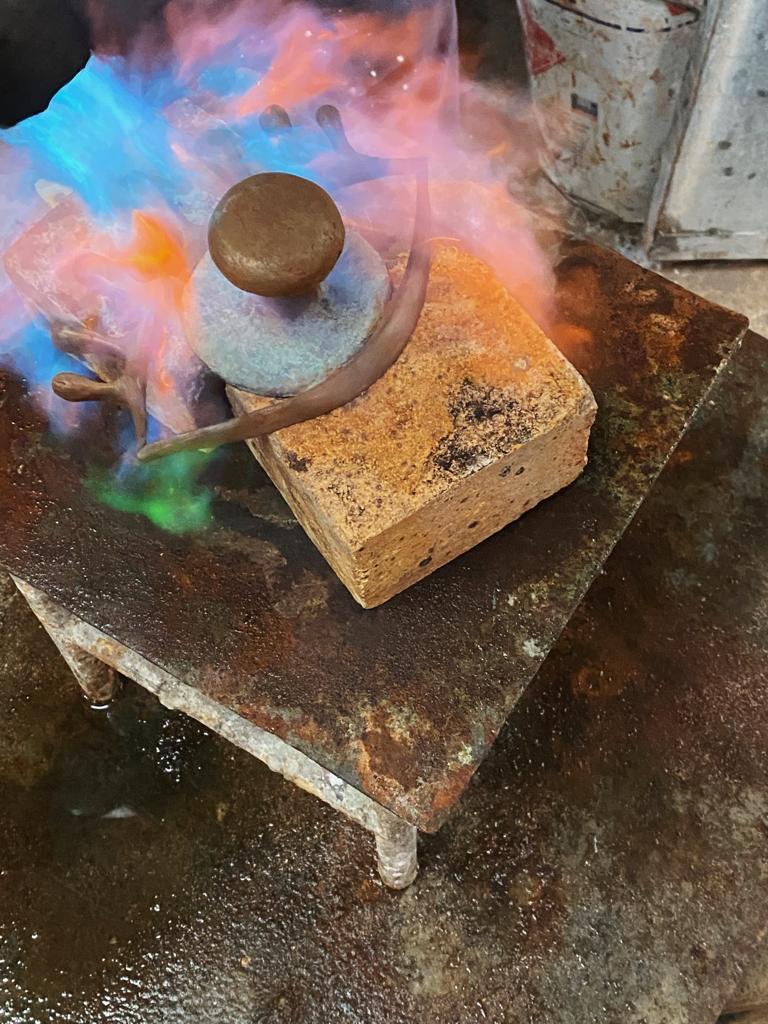
Although it is the only artistic foundry on the islands, with a solid portfolio of door knockers, produced and replicated for boutique hotels, banks and band clubs, it had never produced its own series of creations.
Meanwhile, Lisa identified an interesting niche to develop – contemporary designs for doorknobs and knockers, which are “contextually relevant yet aesthetically appealing”.
The collaboration made perfect sense to both, on several levels. Dubbed Contemporary Traditions, this ongoing collaboration aims to produce series of doorknobs and knockers, which kicked off with an initial four designs: the Monstera deliciosa [Swiss cheese plant] leaf, the scallop shell, and the [male] seahorses, which are customisable as both knobs and knockers, and also a pair of asymmetrical eyes.
The beauty of bronze doorknobs and knockers is perhaps their raw and hand-made feel and finish, Lisa maintains. They are veritable artworks, the creation process taking weeks to complete: from the preparation of the mould ahead of casting to finishing and patination.
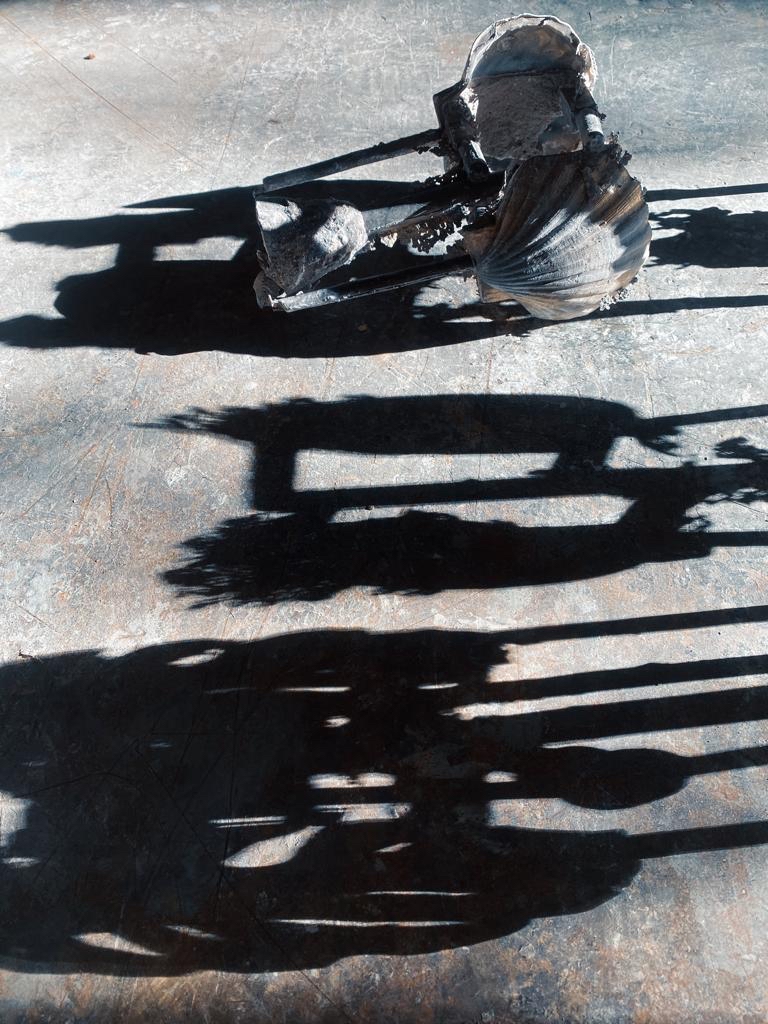
Thanks to the guidance and expertise of Christopher Chetcuti, who has been working at the foundry for some 15 years, these designs, originally sketched and then translated into 3D pieces using plastiline, are produced using the traditional lost-wax method [cera persa].
Christopher’s dexterity with patination has meant each piece is unique – no two artworks are ever identical.
More than just an accessory for a front door, the knockers are functional fine art sculptures.
Discovering the lost-wax process used in bronze casting
Following the research process, Lisa began sketching the designs, taking into account the dimensions of each piece to ensure its suitability to the final material.
The sketches were then transferred into plastiline and the mould-making process began, whereby the original clay design was destroyed to produce a plaster replica from which a ‘negative’ design mould in silicone was produced.
The silicone mould was then filled with wax to replicate the design. Once dried, and the mould carefully removed, the application and attachment of colati, strategically placed cylindrical channels that connect each of its segments, was carried out.
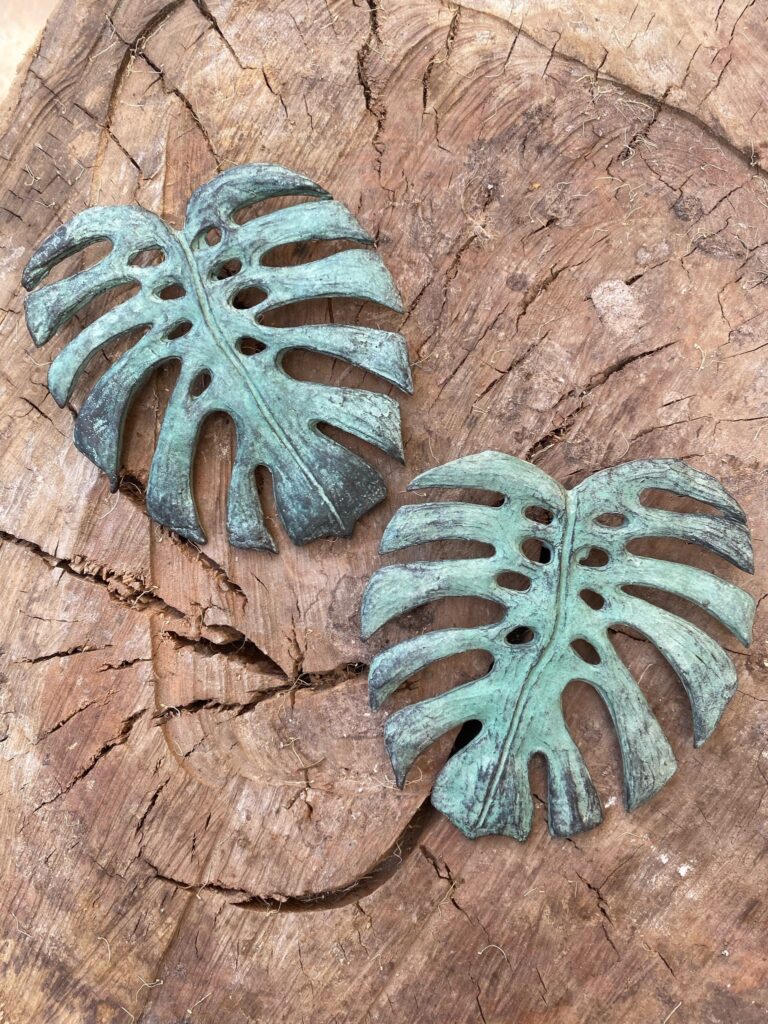
This is done to ensure the complete spread of bronze during the casting process.
The wax piece is then dipped into luto – the material used for the outer investment mould – and it is then fired in the oven in a process that lasts between three and five days.
During this time, the wax melts and the luto mould is fortified ahead of the molten bronze that will be poured into it.
After 24 hours of cooling, the molten bronze can be poured into the investment mould, after which it is left to cool down completely
The investment mould is then broken off and the design released, followed by the careful removal of the colati, the finishing and chasing of the artworks, and finally, the application of the chosen patina.
Funderija Artistika Chetcuti utilises recycled materials at every stage of the bronze casting process until these do not impact the quality and finish of the work.
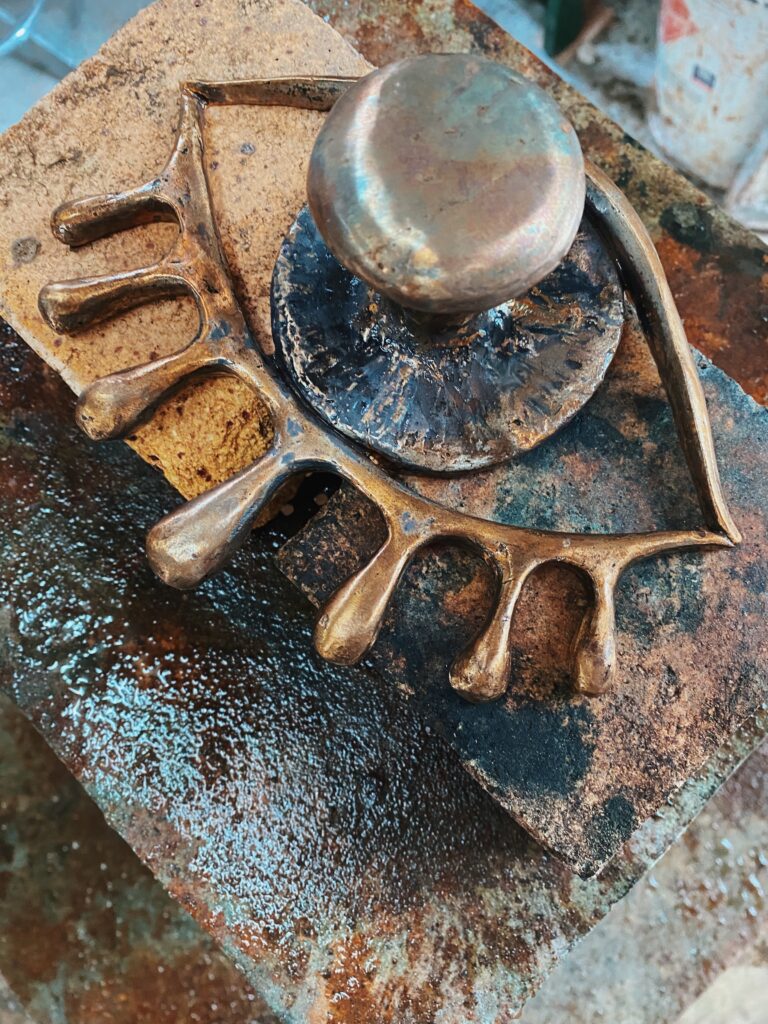
From copper wires for the bronze to excess bronze from damaged artworks, as well as the removed colati, which is melted down again for resuse, to the luto, these are all recycled.
For a handmade and authentic feel, the left and right knobs and knockers were modeled separately, meaning no two are identical, with the exception of the scallop shell.
With some products, such as the seahorses and the eyes, two patinas were used to add to the overall finished quality and effect of the product.